Il mese scorso avevamo scritto di quanto fosse importante per un’azienda, una volta definito il piano strategico, che venisse tradotto in organizzazione, suddividendo i reparti ed analizzando i processi e le procedure per eliminare eventuali criticità operative, colli di bottiglia, duplicazioni o punti di interruzione del dialogo tra le funzioni aziendali. In questa fase l’organizzazione deve apparire fluida ed il processo risultare efficiente nella sua interezza.
Avevamo quindi accennato al metodo Kaizén (=Miglioramento Continuo) e alla filosofia Lean come preziosi alleati per ottimizzare tale organizzazione, incoraggiando la semplificazione e l’efficienza ed eliminando l’ipercomplessità delle procedure, se esse non portano valore a coloro che tali procedure devono seguire.
Oggi, cerchiamo di capire nel dettaglio di cosa stiamo parlando. Il termine “Kaizen” deriva dalle parole giapponesi KAI (=cambiamento, miglioramento) + ZEN (=buono, migliore): insieme significano MIGLIORAMENTO CONTINUO. Il senso moderno della parola ha origine dopo la seconda guerra mondiale nelle fabbriche giapponesi della Toyota dove due consulenti americani, Edwards Deming e Joseph Juran, furono inviati per migliorare la produttività attraverso una serie di tecniche per la gestione della produzione basate sui concetti di miglioramento continuo e sistematico della qualità (=Toyota Production System, o TPS).
Il KAIZEN infatti presuppone un cambiamento continuo e il METODO KAIZEN è dunque l’insieme delle tecniche che permettono di pensare, analizzare e migliorare, attraverso le persone, l’efficacia operativa mirando alla ricerca continua della perfezione senza che ciò richieda grandi investimenti, ma attraverso l’ottimizzazione delle risorse disponibili impiegate per eliminare le inefficienze.
Per riassumere, quindi, possiamo dire che i principi fondanti sono:
- Focus sul miglioramento continuo attraverso piccoli, incrementali cambiamenti.
- Coinvolgimento di tutti i livelli dell’organizzazione, dai manovali ai dirigenti.
- Applicazione quotidiana e costante di piccoli miglioramenti nei processi.
- Enfasi sulla collaborazione, la disciplina e la standardizzazione.
Gli strumenti principali utilizzati per implementare tale metodo sono il ciclo di Deming PDCA (Plan-Do-Check-Act), le 5S (Sort=Semplificare, scegliere e separare; Set in order=Sistemare, ordinare ed organizzare; Shine=Splendere, pulire; Standardize=Stabilizzare e standardizzare; Sustain=Sostenere nel tempo) e i kaizen blitz (eventi intensivi di miglioramento).
Il Lean Thinking, o pensiero snello, pur derivando dal TPS, è stato però codificato e reso popolare dai ricercatori americani Womack, Jones e Roos negli anni 90. Anch’esso applicato inizialmente in ambito di produzione automobilistica, si è però poi diffuso velocemente in una vasta gamma di settori, dall’industria alla sanità e ai servizi. Lo scopo principale è quello di eliminare gli sprechi (=MUDA) creando valore per il mercato. Le forme di spreco considerate in tale approccio inizialmente erano:
- L’eccesso di attività: realizzare attività che non producono valore;
- Il movimento: spostarsi per raggiungere materiali lontano dal punto di utilizzo;
- I difetti: produrre scarti o rilavorazioni;
- La gestione delle scorte: acquistare o produrre materiali in eccesso rispetto al fabbisogno del processo successivo;
- L’eccesso di produzione: produrre più di quanto richiesto dal cliente o dal processo successivo;
- L’attesa: impiegare il tempo in maniera non produttiva;
- Il trasporto: spostare il materiale senza necessità o senza creazione del valore.
In un secondo momento quando il LEAN è stato esteso, diventando una filosofia di gestione, a quasi tutti i settori e non solo a quelli produttivi, si sono delineati 5 principi-guida che hanno poi guidato il modello teorico della produzione snella:
- definire il valore dal punto di vista del cliente; cosa il cliente è veramente disposto a pagare;
- identificare il flusso di valore: identificare l’insieme di azioni che portano a realizzare il prodotto o il servizio (=Value Stream Mapping);
- impostare le attività secondo la logica “pull” e non “push”, ovvero realizzare un’attività solo quando il processo a valle lo richieda;
- far fluire tutte le attività; tutto deve realizzarsi per processi e non per funzioni, senza soste o interruzioni (=just in time, JIT);
- perseguire la perfezione tramite continui miglioramenti (fare kaizen).
Ma perché adottare un approccio LEAN in Azienda? Perché non solo obbliga ogni singola persona, indipendentemente dalla propria funzione, a porre in essere una serie di azioni standardizzate per ottenere migliori risultati dal punto di vista operativo, ma significa anche aumentare competitività e redditività aziendali MENTRE migliora il benessere personale e professionale (e dunque l’efficacia e l’efficienza) dei collaboratori.
A volte, poi, è facile confondere il KAIZEN con il LEAN: questo avviene perché effettivamente tra le due metodologie esistono punti in comune:
- Entrambi gli approcci condividono l’obiettivo di migliorare i processi e aumentare l’efficienza.
- Il concetto di miglioramento continuo è centrale in entrambi i metodi.
- Promuovono la partecipazione di tutti i livelli dell’organizzazione.
Tuttavia è importante anche conoscerne i punti di differenziazione, e cioè:
- Kaizen si concentra su piccoli miglioramenti incrementali e quotidiani, coinvolgendo tutti i membri dell’organizzazione in un processo continuo di miglioramento.
- Lean Thinking ha un focus più ampio sulla riduzione degli sprechi e sull’ottimizzazione del flusso di valore attraverso l’intera organizzazione, utilizzando una serie di strumenti e tecniche specifiche.
In sintesi, mentre il Kaizen rappresenta un approccio culturale e operativo di miglioramento continuo quotidiano, il Lean Thinking offre una filosofia più ampia e strutturata per ottimizzare l’intera catena del valore e ridurre gli sprechi a livello sistemico. Entrambi i metodi si integrano e si completano a vicenda, fornendo una base solida per l’efficienza e la qualità nei processi produttivi e aziendali.
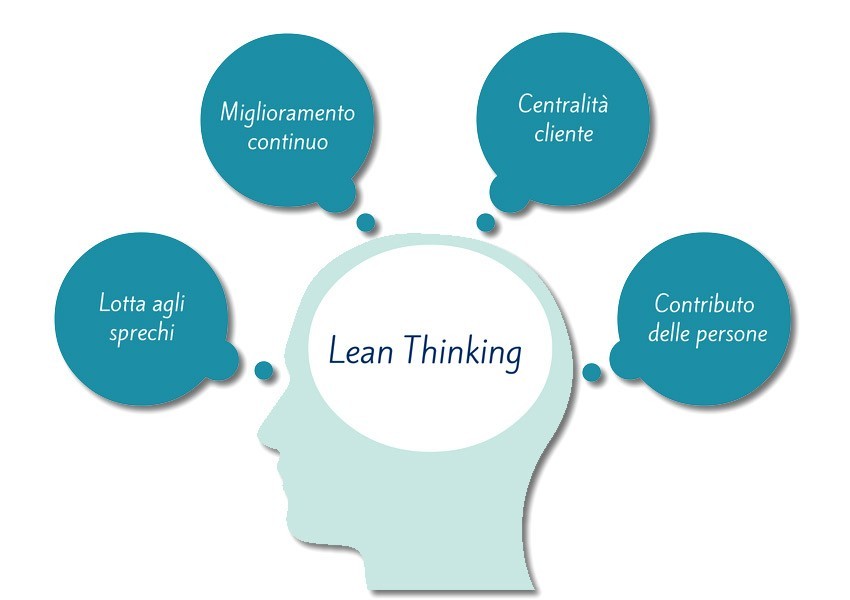